Electric Plastic Molding: Revolutionizing Manufacturing
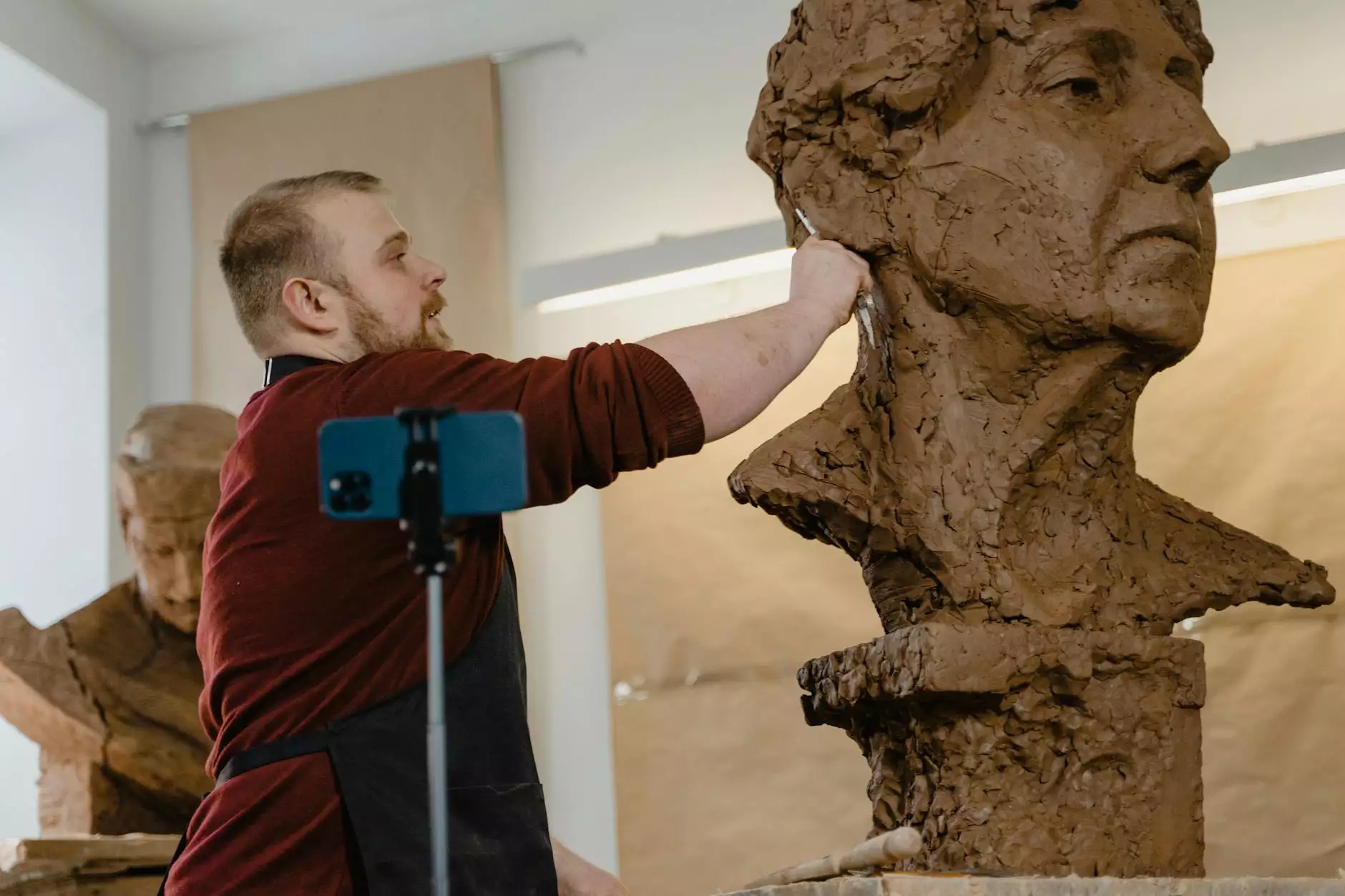
Electric Plastic Molding is a pivotal technology that is transforming the manufacturing landscape, especially within the metal fabrication industry. This article delves into the benefits, applications, and intricacies of this innovative molding technique, helping businesses like DeepMould.net leverage its potential for enhanced efficiency and effectiveness.
What is Electric Plastic Molding?
Electric plastic molding is a method of shaping plastic materials using electric-powered machines. Unlike traditional hydraulic molding, electric molding utilizes servo motors to precisely control the movement and operation of the molding process. This results in greater accuracy, faster cycle times, and lower energy consumption.
The Process of Electric Plastic Molding
The process begins with the heating of plastic pellets until they become malleable. These pellets are then injected into a mold cavity where they take shape. The following steps outline the electric molding process:
- Material Preparation: Plastic resin is prepared and dried to remove moisture, ensuring a high-quality end product.
- Molding Machine Setup: Electric molding machines are set with precise parameters like temperature, pressure, and speed, tailored to the specific plastic type.
- Injection Phase: The heated plastic is injected into the mold under controlled conditions.
- Cooling Phase: The mold cools, allowing the plastic to harden and retain its shape.
- Demolding: The finished product is ejected from the mold, ready for further processing or assembly.
Advantages of Electric Plastic Molding
Electric plastic molding offers numerous advantages over conventional methods, particularly beneficial for businesses in the metal fabrication sector:
- Precision and Consistency: The use of servo motors enhances the precision of injection, resulting in quicker mold changes and more consistent part quality.
- Energy Efficiency: Electric machines consume less energy, reducing operational costs and benefiting the environment.
- Reduced Cycle Times: Faster heating and cooling cycles lead to increased productivity and efficiency in manufacturing processes.
- Lower Maintenance Costs: With fewer moving parts compared to hydraulic systems, electric machines require less maintenance, translating to lower costs.
- Environmentally Friendly: Electric molding reduces energy consumption and waste, aligning with modern sustainable practices.
Applications of Electric Plastic Molding
Electric plastic molding is utilized across various industries due to its versatility:
- Automotive Parts: Producing complex components such as dashboards, bumpers, and interior fittings.
- Electronics: Manufacturing intricate housings and connectors with high accuracy.
- Medical Devices: Creating precision components for medical equipment with strict regulatory standards.
- Consumer Goods: Producing everyday products ranging from kitchenware to toys, requiring durability and precision.
The Impact on Metal Fabrication Businesses
For businesses specializing in metal fabrication, electric plastic molding represents a significant opportunity for integration and growth. As the demand for complex designs and high-quality components rises, adopting electric plastic molding technology can provide a competitive edge.
Enhancing Product Quality
With electric plastic molding, metal fabricators can achieve tight tolerances and intricate designs. This ability to produce high-quality plastic parts means that businesses can offer more comprehensive solutions, integrating both metal and plastic components seamlessly.
Expanding Capabilities
Integrating electric plastic molding into a metal fabrication business opens up new avenues for product offerings. Businesses can diversify their services, catering to new markets and increasing their customer base.
Challenges and Considerations
While electric plastic molding presents substantial benefits, businesses must also consider certain challenges:
- Upfront Costs: The initial investment for electric molding machines can be significant, requiring careful financial planning.
- Training and Expertise: Staff may need specialized training to operate and maintain electric molding machinery effectively.
- Material Compatibility: Not all plastics are suitable for electric molding, necessitating research into material properties.
Future Trends in Electric Plastic Molding
The landscape of electric plastic molding is continually evolving, driven by technological advances and market demands. Some key trends include:
Automation and Smart Technology
Increasingly, manufacturers are incorporating automation and smart technology within electric molding processes. This includes the use of IoT devices to monitor production in real-time, predictive maintenance algorithms, and enhanced data analytics to optimize workflows.
Sustainable Practices
As sustainability becomes a priority, electric plastic molding will likely see innovations aimed at reducing waste and energy consumption. Closed-loop systems that recycle plastic waste and innovations in biodegradable materials are on the horizon.
Conclusion
In conclusion, Electric Plastic Molding is not just a trend but a significant advancement that can redefine manufacturing processes across various industries. For businesses in metal fabrication, embracing this technology can lead to improved efficiency, enhanced product quality, and a competitive edge in a rapidly changing marketplace.
At DeepMould.net, we recognize the importance of adopting such innovative techniques in modern manufacturing. By integrating electric plastic molding into our services, we aim to provide our clients with the best quality and efficiency, paving the way for future advancements in the industry.