The Revolution of Business Through Extrusion Moulding
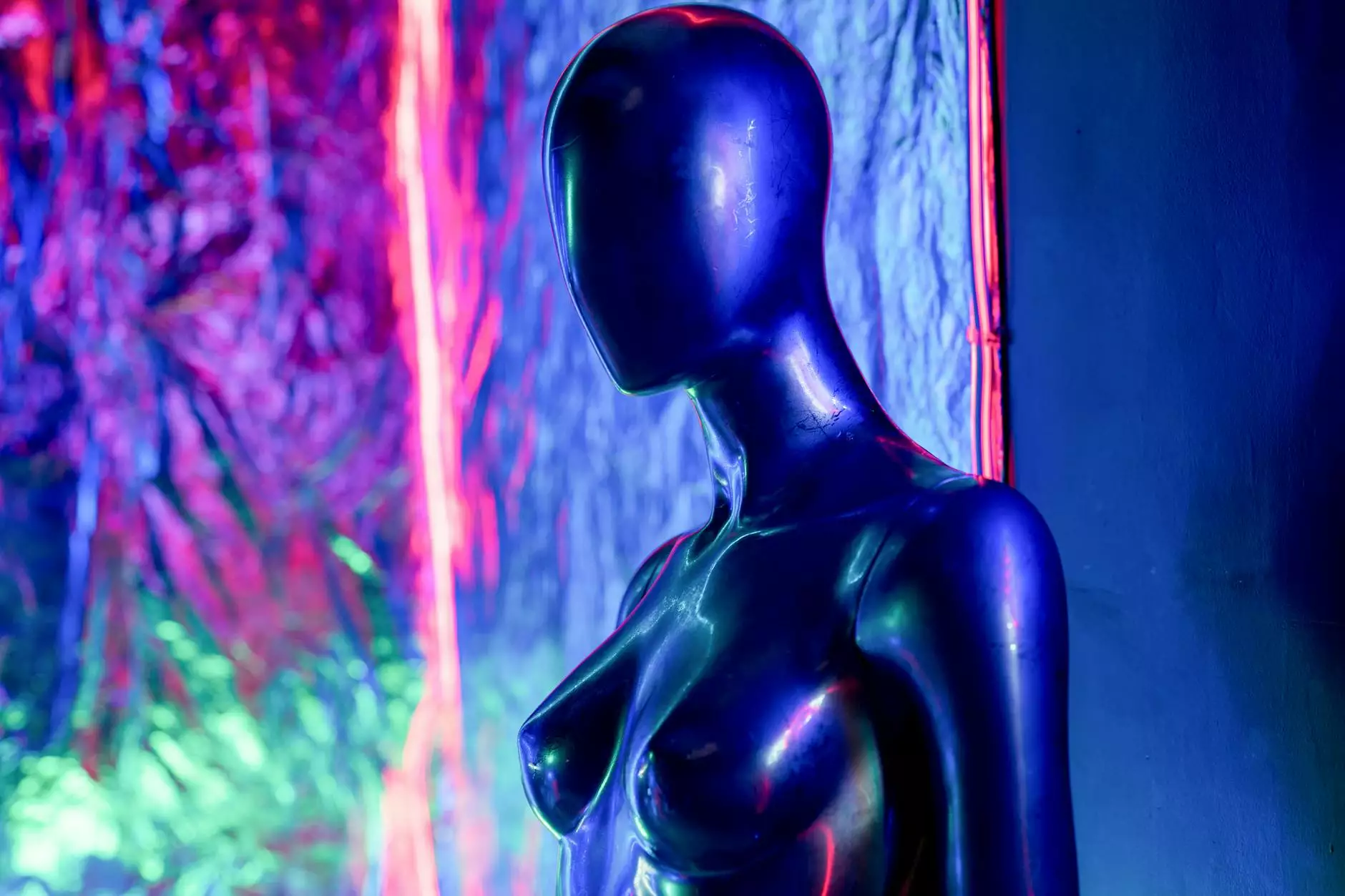
Extrusion moulding stands at the forefront of modern manufacturing techniques, significantly influencing various sectors, including art supplies, product design, and 3D printing. This article delves into the mechanics of extrusion moulding, its applications, and its revolutionary impact on the business landscape.
Understanding Extrusion Moulding
At its core, extrusion moulding is a manufacturing process where raw materials, typically plastics or metals, are melted and formed into continuous shapes. The process involves forcing material through a die, creating products of uniform cross-section. This method is widely celebrated for its efficiency and scalability, making it an ideal choice for various applications.
How Extrusion Moulding Works
The extrusion moulding process can be summarized in several key steps:
- Material Preparation: Raw materials, usually in pellet form, are fed into an extruder.
- Heating: The material is melted through controlled heating within the extruder.
- Extrusion: The molten material is pushed through a specifically designed die, shaping it into the desired form.
- Cooling: The freshly extruded product is cooled, forming a solid shape.
- Cutting: The product is cut into specified lengths for further processing or distribution.
This sequence highlights the streamlined nature of extrusion moulding, whereby consistent products can be manufactured at high speeds and reduced costs.
Applications of Extrusion Moulding
Extrusion moulding is instrumental across various industries. Here are some notable applications:
- Art Supplies: Many artistic materials, including tubes for paint, plastic canvases, and other art tools, benefit from extrusion moulding due to its efficiency and versatility.
- Product Design: Innovative product designs often leverage extrusion moulding to create unique shapes and forms that stand out in the market.
- 3D Printing: In the realm of 3D printing, extrusion moulding provides the basic filament used in the printing process, allowing for high precision and creativity in designs.
The Advantages of Using Extrusion Moulding
Businesses across various sectors choose extrusion moulding for numerous compelling reasons:
- Cost-Effective: The mass production capabilities of extrusion moulding lead to significant cost savings.
- Versatility: A vast array of materials can be used, from plastics to metals, enhancing product diversity.
- Consistency: The process ensures uniformity in product dimensions, crucial for quality assurance.
- Environmental Sustainability: Many companies utilize recyclable materials in their extrusion processes, contributing to sustainability efforts.
Case Studies: Extrusion Moulding in Action
To truly understand the impact of extrusion moulding, let's explore a few case studies that illustrate its effectiveness:
1. Art Supplies Innovation
A leading manufacturer of art supplies utilized extrusion moulding to create unique, ergonomic paint tubes. By designing the tubes with a new extrusion die, they enhanced the user experience, allowing artists to control the flow of paint effortlessly. This innovation not only won awards but also increased sales significantly.
2. Redefining Product Design
A furniture design company integrated extrusion moulding to create custom furniture components. Each piece could be produced in various colors, finishes, and shapes, catering to diverse customer preferences. This capability helped them stand out in a competitive marketplace while streamlining their supply chain.
3. Enhancing 3D Printing Materials
A startup focusing on sustainable 3D printing developed a new range of filaments through extrusion moulding, using recycled plastics. This initiative attracted eco-conscious customers and positioned them as market leaders in sustainable 3D printing solutions.
The Future of Extrusion Moulding in Business
The future of extrusion moulding looks promising, with ongoing advancements in technology and material science. Some anticipated trends include:
- Biodegradable Materials: The shift towards using biodegradable polymers will enhance the sustainability of products created through extrusion.
- Smart Extrusion Processes: Incorporating AI and machine learning into extrusion processes for better quality control and predictive maintenance.
- Customization: Increased demand for customized shapes and designs will drive innovation in die manufacturing and extrusion techniques.
Challenges in Extrusion Moulding
While extrusion moulding offers numerous benefits, it is not without challenges:
- Initial Setup Costs: The design and manufacturing of custom dies can be expensive, posing a barrier for smaller businesses.
- Material Limitations: Not all materials are suitable for extrusion, which can limit product options.
- Process Sensitivity: Variations in temperature and pressure must be precisely controlled to ensure product consistency.
Optimizing Your Business with Extrusion Moulding
Businesses looking to leverage extrusion moulding can take several steps to optimize their operations:
- Invest in Quality Machinery: Selecting high-quality extruders that meet the specific needs of your business can enhance efficiency.
- Skilled Workforce: Training employees to understand the intricacies of the extrusion process is vital for achieving optimal results.
- Research and Development: Continuous investment in R&D will lead to innovative applications and materials in extrusion moulding.
The Role of Arti90 in Advancing Extrusion Moulding
As a leader in the fields of art supplies, product design, and 3D printing, Arti90 is at the forefront of leveraging extrusion moulding technology. By manufacturing high-quality products that meet the needs of modern creators, Arti90 is setting new standards in the industry. The commitment to innovation and sustainability positions Arti90 as a champion for businesses looking to evolve their processes.
Conclusion: Embracing Extrusion Moulding for Business Growth
In summary, extrusion moulding plays a pivotal role in transforming businesses across various sectors. As companies seek efficiency and innovation, embracing this manufacturing process can provide a competitive edge. With the evolution of technology and materials, the future of extrusion moulding looks brighter than ever, and businesses that adapt will undoubtedly thrive in this dynamic landscape.
For more information and inquiries, visit Arti90.com and explore how extrusion moulding can redefine your production processes today.